A brief history of bell foundries
In the Middle Ages, bellmakers would often travel from village to village, bringing with them their know-how and skill to cast bells in molds near a cathedral or church. Building onsite furnaces in pits at the base of these structures solved a very practical issue: the monolithic weight and challenge of moving bells. Thousand-pound bells could be lifted from the pit directly into the tower, saving poor mules the burden of carting them across rough terrain.
When connections and transportation between cities improved, bellmakers set up shop in dedicated facilities called foundries, allowing them to better control the extreme temperatures needed to melt metal and create long-lasting bells. In times of war, these foundries might have been relied upon to make cannon and weaponry, but while those needs have diminished, bellfounding remains.
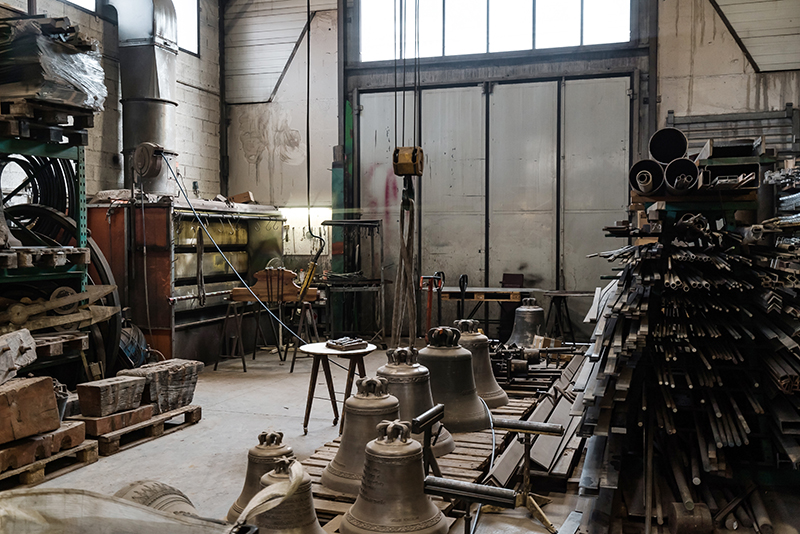
Image: View inside a bell foundry.
Foundries cast bells for all manner of installations: churches, schools, municipal buildings, clock towers, ships, trains, and even farms – roughly 300 different foundries are known to have operated on American soil. Bell foundries often regularly supply bell fittings and replacement parts, while further consulting on tower installations, inspections, ongoing maintenance, and historic bell restoration projects.
Where a bell was cast (the foundry) says a lot about how it was made. From the casting process to the composition of bronze, and from bell tuning to decoration, the imprint of the bellmaker is felt at every turn. Even the very shape of a bell can distinguish its provenance. Bellfounding is both an art and a science that relies on the history and tradition of its craft, while continuing to evolve and redefine its place in our society.
Section image: A craftsman polishes a newly-cast bell at the Van Bergen bell foundry in Heiligerlee, Netherlands, on Nov. 11, 1949.